Gli spazi, l’aria e l’umidità sono certamente dei fattori che creano stress al viaggiatore soprattutto per quello che riguarda l’umidità interna spesso insufficiente a garantire un adeguato livello di umidità relativa. In genere l’umidità nelle cabine degli aeroplani è inferiore al 10%, ciò non comporta rischi per la salute, ma può causare secchezza cutanea e disagio a occhi, bocca e naso.
Su un articolo riportato dal The Economist, si legge che molti dei disagi legati al volare derivano proprio dalla pressione atmosferica e dall’umidità. A un’altezza di diecimila metri, la pressione dell’ossigeno nell’atmosfera è troppo bassa per la vita umana così gli ambienti all’interno degli aerei devono essere pressurizzati.
Gli standard FAA impongono di mantenere la pressione dell’aria uguale a quella che si otterrebbe naturalmente all’altezza di 2400 metri con un’umidità relativa bassa. In genere questo fenomeno non dovrebbe causare grossi danni alla maggior parte delle persone ma può essere un rischio per persone che presentano già problemi cardiaci o respiratori generando mal di testa, vertigini, stanchezza, ecc…
Il motivo per cui si impone una presurizzazione pari a 2400 metri con un’umidità molto bassa è dovuto al fatto che una pressione pari al livello del mare sottoporrebbe a uno sforzo enorme l’aereo, inoltre le strutture in alluminio degli aerei di vecchia generazione si corrodono in ambienti troppo umidi.
Oggi grazie alle nuove tecnologie è possibile migliorare il confort all’interno degli aerei utilizzando materiali compositi formati da una matrice polimerica in cui vengono inserite delle fibre, come quelle di vetro o di carbonio per ottenere dei nuovi materiali da costruzione sempre più resistenti, performanti e leggeri che possano sostituire quelli tradizionali, come l’acciaio e l’alluminio.
In campo aeronautico i materiali compositi sono molto utilizzati soprattutto grazie al risparmio in peso unito all’alta resistenza a fatica e alla corrosione. Basta pensare che risparmiando un chilogrammo su un aero medio-piccolo come l’Airbus A320, in un anno si risparmiano circa 300 kg di carburante. Con l’impiego di CFRP (fibre di carbonio in resina polimerica) si arriva ad una riduzione in peso del 20% rispetto all’alluminio. Grazie all’elevata resistenza garantita dalla fibra di carbonio è stato possibile alzare la pressione interna, corrispondente a 1.800 metri sul livello del mare e aumentare il tasso di umidità, garantendo una migliore comodità per i passeggeri, soprattutto nelle lunghe percorrenze.
Due sono i gruppi più importanti a livello mondiale che producono aerei di nuova generazione, la statunitense Boeing con il Boeing 787 e il consorzio europeo Airbus con l’Airbus A-350 e l’Airbus A-380.
Il Boeing 787 è realizzato al 50% in fibra di carbonio e permette di risparmiare circa il 20% in meno di carburante con un confort maggiore per i viaggiatori. Ha sedute più ergonomiche e gli oblò grandi riducono la sensazione di “chiuso” che può generare un senso di claustrofobia.
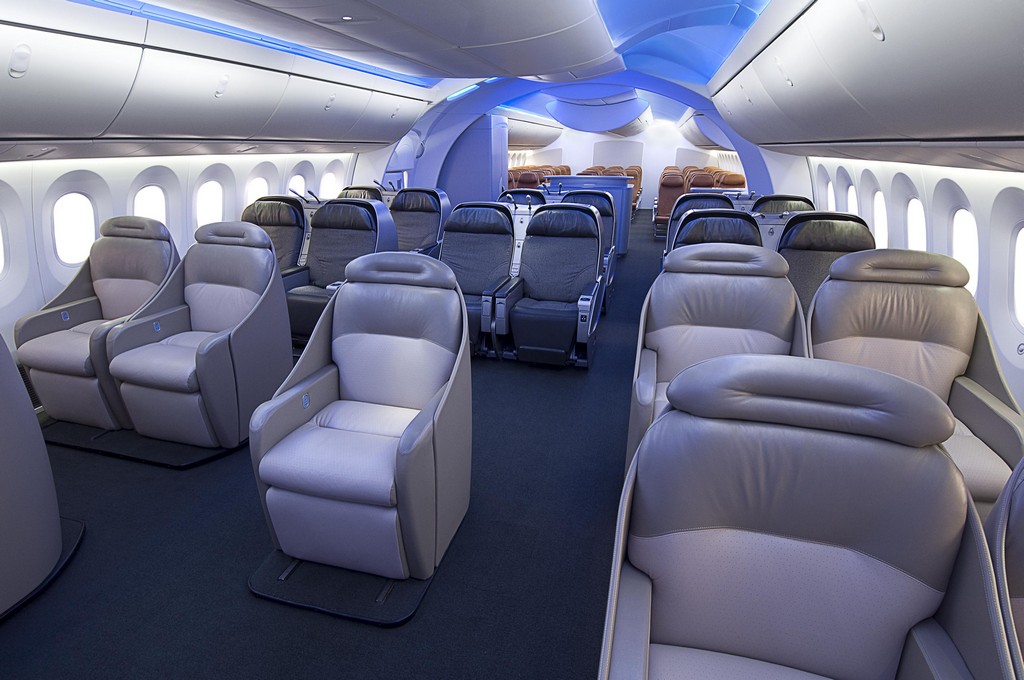
L’Airbus A-350 è realizzato con la fusoliera in fibra di carbonio, mentre i comandi pneumatici e idraulici sono stati sostituiti dall’elettronica, riuscendo a tagliare i consumi del 25% con un aumento del confort dei passeggeri.
L’Airbus A-380 è il più grande aereo mai commercializzato al mondo, si affida a componenti che ne riducono drasticamente il peso e gli consentono di trasportare 555 passeggeri per 15.000 km senza scalo. E’ costituito per circa il 25% da compositi strutturali, utilizzati per le ali, sezioni di fusoliera, impennaggio di coda e porte.
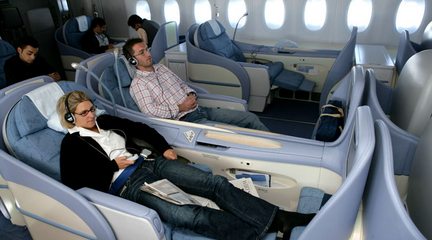
Grazie a questi nuovi materiali viaggiare su questi aerei diventa più piacevole e i passeggeri arrivano a destinazione più riposati e senza stress.