Il Progetto Cassiopea, situato nell’area di Gela, rappresenta un intervento complesso e cruciale per l’approvvigionamento energetico nazionale.
Con un investimento di circa 900 milioni di euro, il progetto mira ad estrarre e trattare il gas naturale dai giacimenti sottomarini Argo e Cassiopea, nel Canale di Sicilia, per immetterlo nella rete nazionale.
Quattro pozzi e un impianto onshore
“Cassiopea” costituisce azione operativa della strategia ENI di promuovere il gas naturale come energia a basse emissioni. L’intervento ha previsto la realizzazione di 4 pozzi sottomarini e un impianto di ricezione, trattamento e compressione del gas naturale.
Il gas estratto dai giacimenti Argo e Cassiopea, trattato nell’impianto di Gela, avrà una capacità che supererà di sette volte l’attuale produzione siciliana e coprirà oltre il 30% del fabbisogno regionale. L’estrazione avverrà completamente sott’acqua, senza impatti visivi o emissioni, e il gas sarà inviato tramite una linea sottomarina di 60 km all’impianto di Gela, da dove sarà distribuito nella rete nazionale Snam.
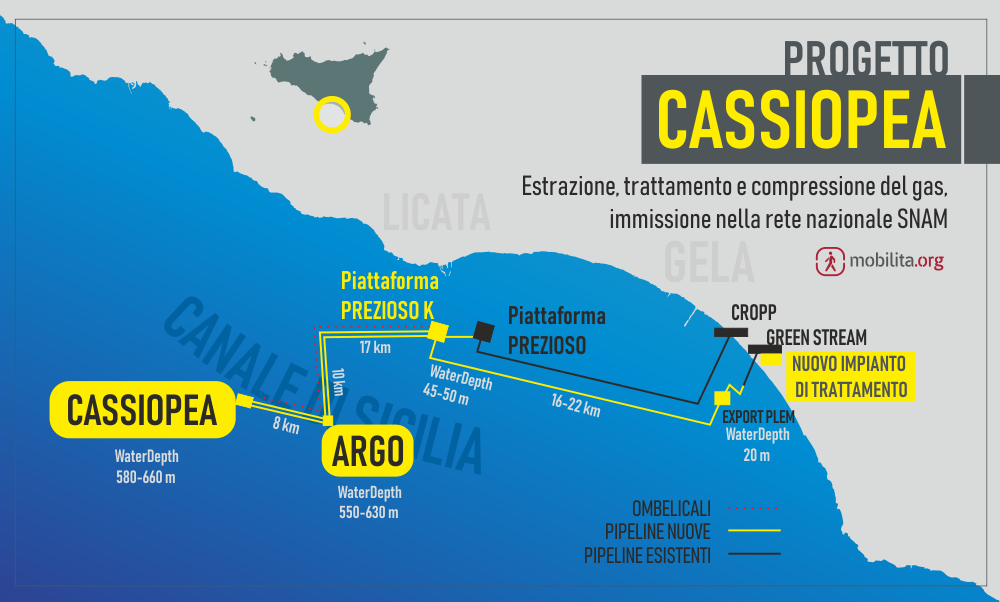
Per conoscere in modo più approfondito i dettagli di questo progetto sulla costa siciliana abbiamo incontrato “Gradito Oleodinamica” di Gela, società specializzata in oleodinamica e tessera di un mosaico di aziende, professionisti e maestranze che hanno preso parte all’intervento. Ci accompagna nel racconto l’Ing. Giuseppe Guida, Project Manager della commessa e direttore tecnico di Gradito Oleodinamica.
Questo progetto è fondamentale per il territorio, non solo perché contribuisce alla sostenibilità energetica italiana, ma anche perché valorizza la manodopera locale e garantisce standard tecnologici elevatissimi
Ing. Giuseppe Guida
Piping e apparecchiature: il ruolo di Gradito Oleodinamica
Dal 2022 al Dal 2022 al 2024, la Gradito Oleodinamica ha avuto un ruolo centrale nella fase onshore del progetto, laddove è stato realizzato l’impianto di trattamento e compressione del gas: dalla prefabbricazione all’installazione delle tubazioni, fino al montaggio delle unità di compressione del gas all’interno della bioraffineria di Gela.
Ing. Guida: “Sino a Luglio del 2024 abbiamo lavorato con precisione su circa 20.000 pollici di saldature e circa 3 km di tubature, sottoponendo ogni pezzo a i rigorosi controlli necessari, come esami visivi, test a liquidi penetranti e radiografie”.
L’azienda ha inoltre curato la parte elettro-strumentale dell’intervento, installando sistemi di illuminazione, sensori, impianti antincendio e dispositivi di controllo.
Ing. Guida: “Il nostro contributo ha richiesto un’attenzione particolare alla sicurezza e all’affidabilità, usando tecnologie all’avanguardia e materiali conformi alle normative PED e ATEX”.
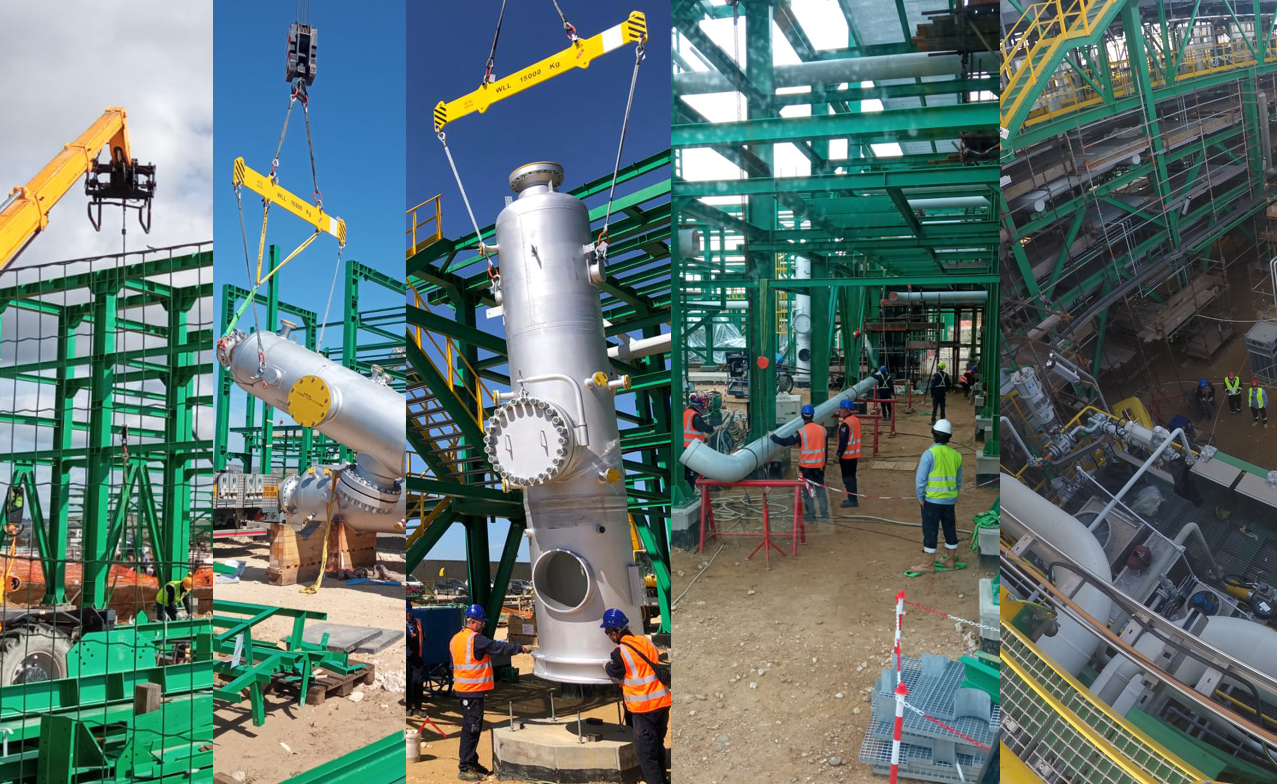
L’impianto a terra costituisce l’approdo per il gas proveniente dai giacimenti in mare e garantisce che il prodotto finito sia immesso nella rete di distribuzione nazionale secondo precisi standard di qualità e pressione di linea.
Le apparecchiature adibite a processare i fluidi sono state commissionate a diverse aziende e, unitamente al piping che le organizza nello spazio e sorregge, vanno a comporre un doppio treno di compressione di cui ENI si avvarrà nelle attività di esercizio.
A differenza di tanti altri casi, in cui questo sistema impiantistico viene localizzato nelle piattaforme in mare, nel progetto Cassiopea si è scelto di ricorrere alla tecnologie più mature e affidabili direttamente a terra, all’interno della bioraffineria di ENI.
Spazi ristretti e oltre 140 unità lavorative
Contrariamente a quanto si possa pensare, l’area di cantiere in cui è stato realizzato l’impianto di compressione non godeva di chissà quali ampi spazi.
Ing. Guida: “L’area di lavoro era di appena 50×50 metri. Questo ha comportato un coordinamento meticoloso tra le squadre per rispettare i tempi e garantire la sicurezza, soprattutto durante le operazioni di sollevamento, quando gran parte del personale doveva sgomberare il cantiere”.
Nonostante le complessità, il progetto si è distinto per un risultato straordinario: gli indicatori di performance KPI hanno messo in evidenza il raggiungimento dei target HSE aziendali, del cliente e della committente rispettando il “Patto per la Sicurezza”.
Ing. Guida: “È un dato di cui siamo molto orgogliosi, frutto di procedure rigorose e di una formazione continua del personale”.
Collaudi e sostenibilità nel progetto Cassiopea
Alle fasi costruttive segue un attento processo di test della strumentazione installata. Il collaudo avviene mediante l’immissione di acqua in pressione, successivamente scaricata, che consente al personale specializzato di monitorare le performance di ogni singolo componente e segnalarne eventuali malfunzionamenti.
Il Progetto Cassiopea si inserisce di fatto nella strategia di riqualificazione della raffineria di Gela, trasformata in bioraffineria, e punta a ridurre l’impatto ambientale.
Ing. Guida: “Tutte le acque utilizzate per i collaudi delle tubazioni vengono trattate con un antibatterico e riutilizzate, per minimizzare lo spreco. È un piccolo esempio di come ogni dettaglio del progetto sia stato pensato per garantire sostenibilità ed efficienza. Nei dettagli si fa la differenza, per questo in azienda facciamo formazione continua al nostro personale, affinchè nulla sia demandato al caso, anche e soprattutto nelle fasi manutentive”.
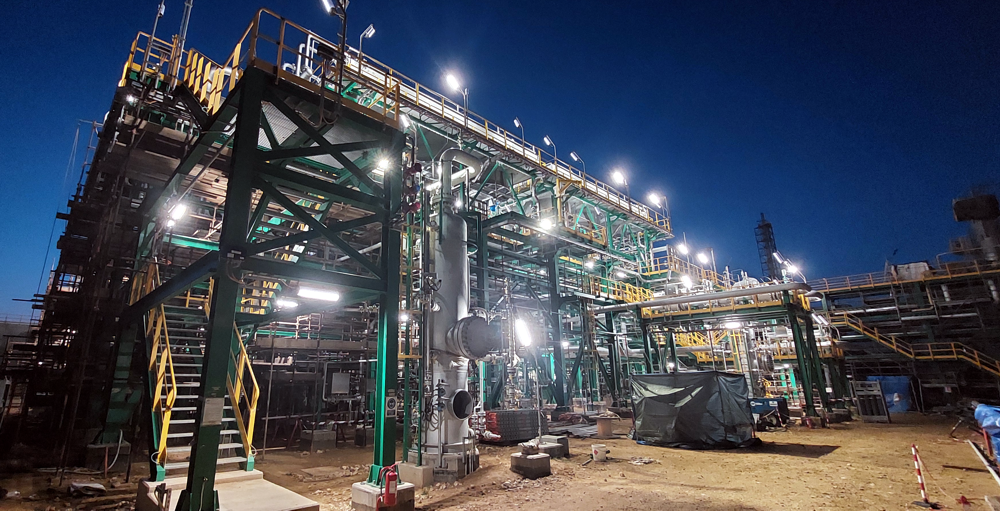
“La riunione delle 5”: il coordinamento Renco
Ammirare la complessità di queste realizzazioni lascia presagire lo spessore della governance necessaria a indirizzare e governare l’intero intervento. Di questo affascinante e delicato incarico ne parliamo insieme ai rappresentanti di RENCO Spa, società leader nel settore dell’ingegneria e main contractor del progetto Cassiopea, curatrice della progettazione dell’impianto e del coordinamento.
Renco partecipa al progetto come membro di un Raggruppamento Temporaneo di Imprese (RTI) insieme a Solar Turbines, rappresentando in Italia l’azienda statunitense, unica al mondo a produrre turbo generatori e turbocompressori in catena di montaggio.
L’Ing. Fabio Verdini, Project Manager di Renco, ci racconta i momenti clou dell’intero iter.
Ing. Fabio Verdini: “Le prime difficoltà sono natLe prime difficoltà sono nate contestualmente all’ottenimento di alcuni permessi. Una volta superate ci siamo fermati per il COVID-19. Alla nuova ripartenza nel Gennaio 2022 è susseguita la guerra in Ucraina che ha innalzato drasticamente i costi dell’energia e delle forniture. Soltanto grazie ad una vera simbiosi che si è realizzata con la Gradito Oleodinamica e le altre società coinvolte, è stato possibile ricreare una partnership efficace a superare ogni criticità”.
Nei suoi momenti di picco, il team di lavoro ha registrato il coinvolgimento di 143 unità.
Ing. Fabio Verdini: “Nelle fasi clou facevamo il punto ogni pomeriggio alle 5. Oggi ricordo con un sorriso quei momenti frenetici, in memoria di sforzi e sacrifici di cui soltanto i risultati ottenuti ci hanno ampiamente ripagato”.
“Full operation”: il collegamento al dispaccio
Come accennato in precedenza, l’impianto in fase di commissioning procede nella pressurizzazione del gas, consentendo al team di lavoro la verifica di tutti i funzionamenti e il rispetto dei parametri dettati dalla normativa. Ogni piccolo disservizio richiederà un intervento di ripristino.
Con l’Ing. Alessandro Strada di Renco, Commissioning leader dell’intervento, ripercorriamo il percorso del gas, dal giacimento sino alla rete distributiva nazionale.
Ing. Strada: “Dai pozzi Argo e Cassiopea il gas viene prelevato ad una pressione di 50 bar. Per essere introdotto nella rete nazionale SNAM la pressione dovrà raggiungere il valore di 60 bar, come richiesto da SNAM. Questo impianto ci consentirà di raggiungere un valore di picco di 75 bar. Negli anni, man mano che il pozzo andrà scaricandosi, diminuirà la pressione in estrazione e aumenterà quella nell’impianto”.
Ma torniamo al commissioning.
Ing. Strada: “L’Impianto è diviso in due treni di compressione: il secondo funge da backup del primo. Questo consente l’esercizio senza interruzioni anche in fase di manutenzione di uno dei due. A dicembre del 2024 Cassiopea è stato dichiarato in “full operaton” e quindi collegato al dispaccio.
A fine Gennaio del 2025 eseguiremo dei test di performance, in cui vengono lasciati entrambi i treni in funzionamento al fine di non riscontrare alcun problema in un arco temporale di almeno 72 ore. E’ una procedura standard nell’ambito dell’ Oil&Gas per raggiungere le performance dichiarate (pressione, aspirazione, temperature, etc.) e ottenere i relativi certificati prestazionali”.
Un progetto di “disponibilità”
Anche a regime, questi impianti richiederanno risorse affinchè l’esercizio non venga mai pregiudicato. La pianificazione delle attività manutentive e la prevenzione degli imprevisti, unitamente al monitoraggio della sicurezza, scandiranno la vita di questa infrastruttura.
“Questo progetto è un perfetto esempio di come il lavoro di squadra e la professionalità possano fare la differenza” conclude l’Ing. Guida di Gradito Oleodinamica.
Il Progetto Cassiopea rappresenta una best practice per l’approvvigionamento energetico italiano, ma anche un modello di collaborazione tra eccellenze, di cui vogliamo sottolineare l’aspetto umano oltre che professionale.
La rappresentazione di un impegno profondo e costante, caratterizzato da sfide, relazioni intense e disponibilità, che ogni professionista ha reso ad ogni suo collega, al fine di superare ogni criticità nel segno del bene comune.
Credits foto: Gradito Oleodinamica